Weighing and mixing of A1
A1 is a combination of A1 Liquid and A1 Powder in the mixing ratio: 1 part A1 Liquid and 2 parts A1 Powder (1:2). This is always based on weight.
Mixing can be done with a stirring stick (small quantities) or with a High Shear mixer. First, start stirring the A1 Liquid and gradually add the A1 Powder. The A1 is ready when all lumps have disappeared. Mixing takes about 1 minute. Try to mix with as less air bubbles as possible in the A1 by keeping the mixer head under the surface.
1.0 Processing time.
After mixing, the standard processing time is 20 – 25 minutes. If a shorter or longer processing time is required, A1 additives can be added.
2.0 Settling time.
A1 is a water-borne product. Residual moisture must evaporate to obtain the final properties. The time required for this is highly dependent on external factors such as the size of the object, temperature and humidity. If the object is laminated or cast in a mould, it can already be removed from the mould as soon as the strength is sufficient to withstand the forces that occur during this process. The product will reach the optimal strength outside the mould.
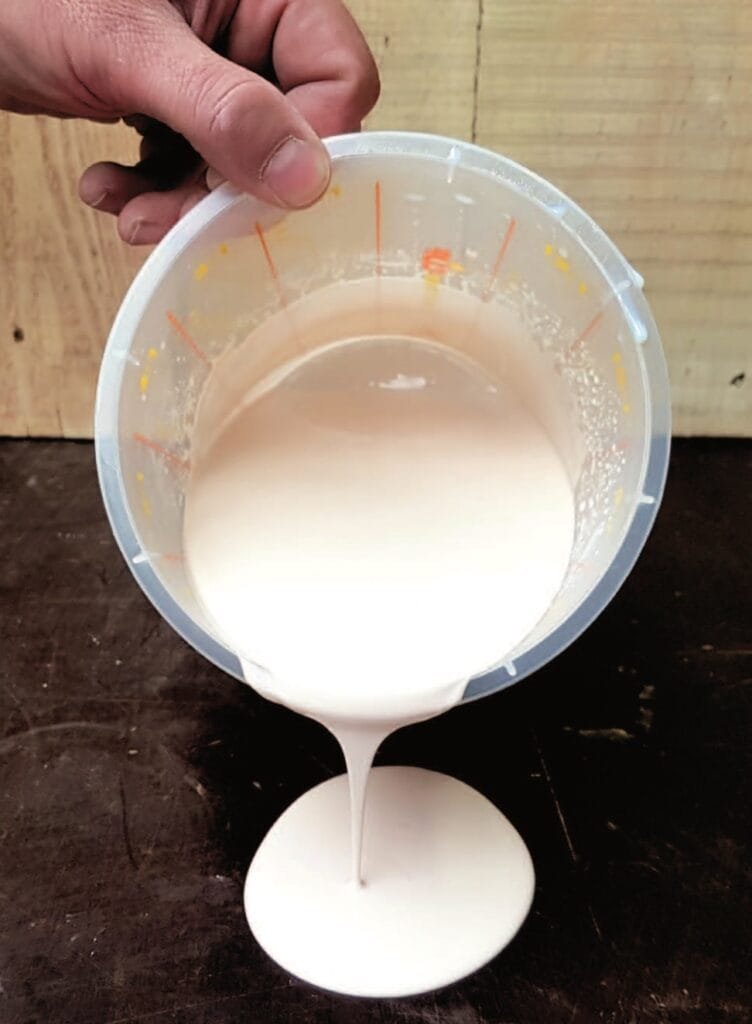
3.0 Can I change the thickness of A1 by adding more A1 Powder or A1 Liquid?
No, keeping the ratio between the A1 liquid and A1 powder is essential for the A1 to react properly. Adding more A1 powder to increase the thickness of A1 should never be done. Also adding more A1 liquid to make the A1 more fluid should be avoided.
4.0 Calculation of A1 needed.
When applying 1 layer of A1 of 1 mm thickness you will use 1.75 kg A1 per m² (1 liter A1 = 1.75 kg).
In a mould you normally work with a first layer of 1 to 2 mm. Next, we advise to use 3 layers of A1 Triaxial fibre. In order to achieve this you will have to apply 4 layers of A1 of 1 mm. Normally in a mould we thicken A1 for the first layer with Thix A. Make sure this layer is hardened before applying the next layers to avoid print through of the A1 Triaxial fibre. Use 1 layer of A1 between your hardened first layer and the first layer of A1 Triaxial fibre in order to make a proper bonding.
As an example needed for a project of 5 m²:
– 2 mm 1st layer.
– 4 layers of 1 mm A1 in order to apply the 3 layers of A1 Triaxial fibre.
Total 6 mm of A1 x 1.75 kg per layer x 5m² is 52,5 kg of A1, consisting of 17.5 kg A1 Liquid and 35 kg A1 Powder.
Be aware that this is an indication and not a general rule.
5.0 The A1 Liquid and the A1 Powder have different batchnumbers. Can I still use them?
When producing A1 we always try to achieve our standaard setting time between 20 and 25 minutes. This means that your working time is about 20 minutes before A1 start to harden.
As our A1 powder is a natural mineral product it varies in reaction time, which we can influence by adjusting our A1 liquid. This means that in order to get a working time of 20 minutes you need to make sure you use the same batchnumbers of the A1 liquid and A1 powder. Normally this will be a 3 letter combination.
Using A1 liquid and A1 powder with different batchnumbers is possible however the working time might be longer or shorter than our standard 20 minutes. That’s why we suggest to do a first small test by mixing 200 grams of A1 powder with 100 grams of A1 liquid. You can check in this way for yourselves the working time.
6.0 Settling tank.
The settling process also continues under water, which is why we recommend removing the tools from water immediately after cleaning. Use a separate bowl of water to clean tools and hands where you can let the A1 sink (minimum 24 hours). After 24 hours, surface water can pass through the sink. The A1 sediment can be left to dry, be disposed of with the residual waste or be reduced and processed as filler (max 1/3). Always follow local regulations.
7.0 I have spots in my castings. How can I solve this?
The three most found reasons why you can have spots in your castings are:
- What you see are A1 powder particles that are not fully mixed into the A1 liquid. Reasons for this can be: a) not using our High Shear mixer, b) High Shear mixer is not cleanend after use and is full of cured A1 so it does not mix properly anymore, c) the mixing duration is to short or d) the A1 powder has been in contact with water(drops), which creates hard particles which will be not be mixed into the A1 liquid anymore.
- Pigments and especially powder pigments sometimes are not mixed properly into the A1. This might result in spots as well.
- A1 Extra White is more sensitive to spots as the balance between de A1 Extra White Powder and the A1 Extra White liquid is more sensitive than our standard A1. Contact us when you are working with A1 Extra White, have checked the suggestions above but still have spots in your castings.
8.0 One of our customers asked us about the A1 resin and powder he purchased 5 years ago. Asks if it is still good to process?
It probably will still work if stored in a not openend package. A small test with 200 grams of A1 liquid and 400 grams of A1 powder, to determine if the A1 still reacts/hardens is the most important test your customer can do. It will probably take more time for the A1 starts to cure. This should be within 40 minutes.
9.0 Does A1 (Acrylic One) Rotation also harden when the mould is closed off from air?
A1 and also A1 Rotation does not need air to harden and will therefore also react and harden without any problems in a closed mould. The response time is longer than our standard A1.
You can also use the remaining A1 Rotation in the mixing bowl to determine when the A1 Rotation has hardened. In order to prevent any damp spots, it is advisable to demould at least the same day. Because fiber reinforcement is not possible, it is advisable to demould carefully because the A1 rotation will still be fragile.
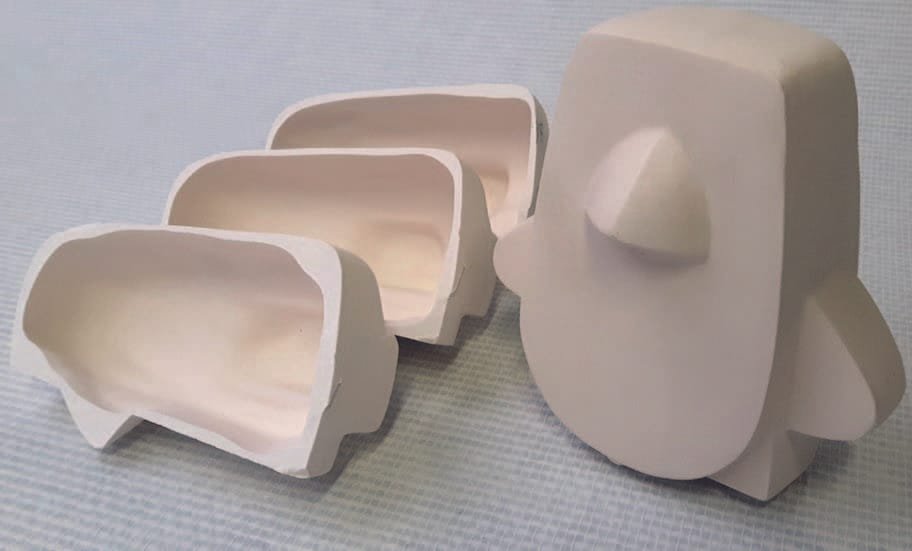
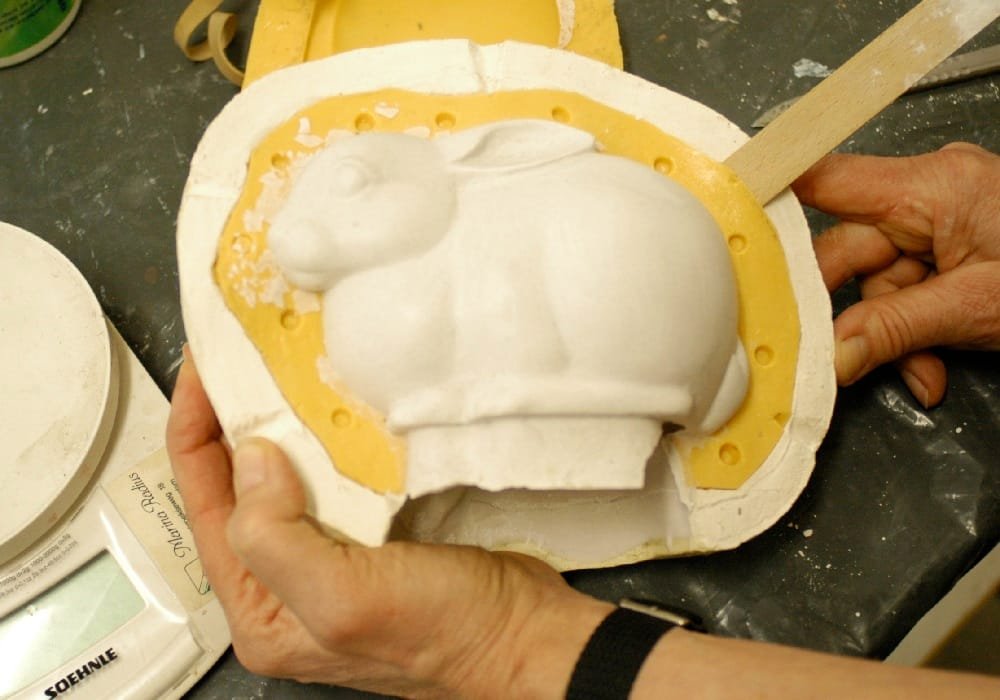
10.0 Why does the A1 object become more shallow after demoulding?
A1 is a water based material and during curing it releases water from the A1 object. Directly after demoulding the A1 object does still contain quite some water which results in a more intense colour of the A1 object. When demoulded the A1 object starts to release its water to the air resulting in losing some of its intense colour. A sealer of coating will restore some of the intense colour but not all.
If the exact tone of the colour of the A1 object is essential, make sure you examine it only after you have given it a chance to release its water to the air. This might take a few days.
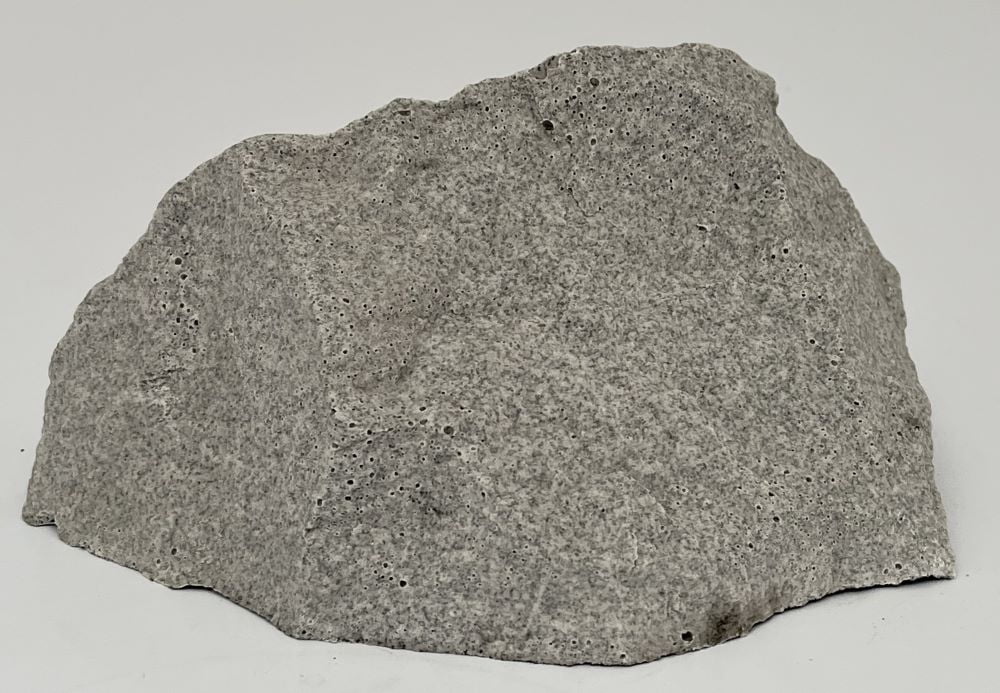
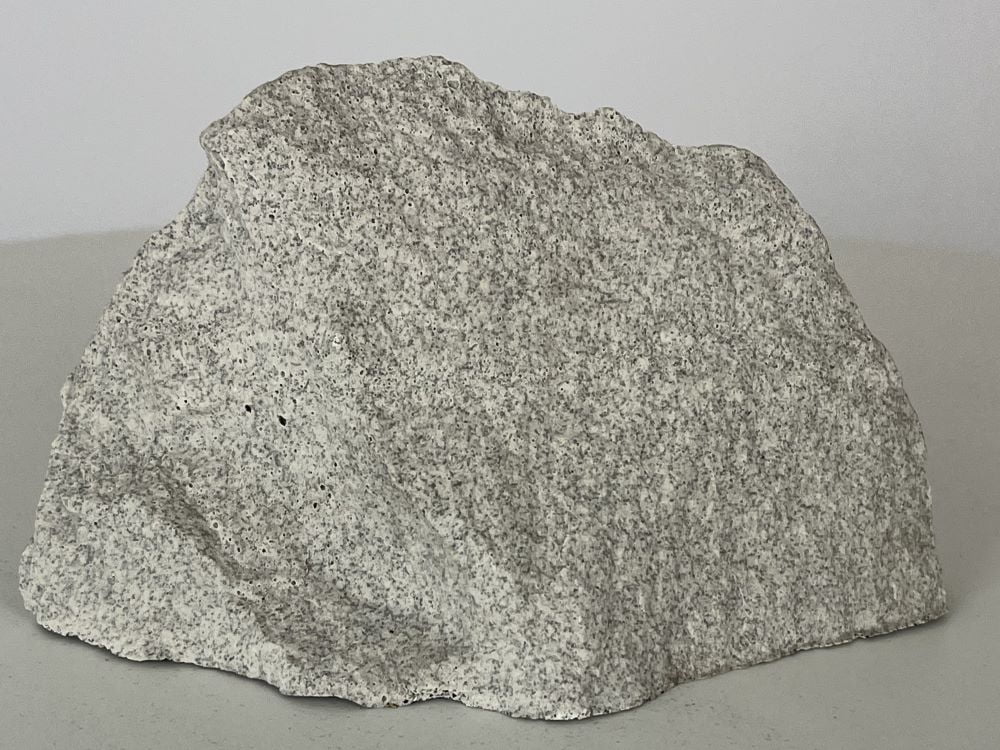
Instruction video
Instruction sheet
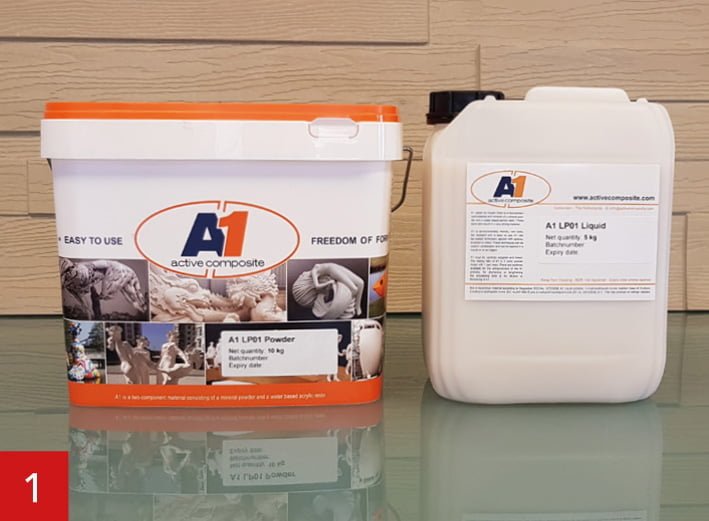
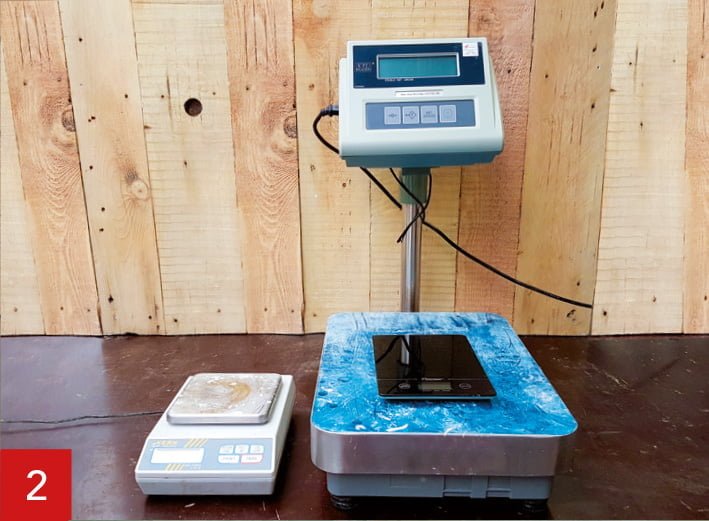
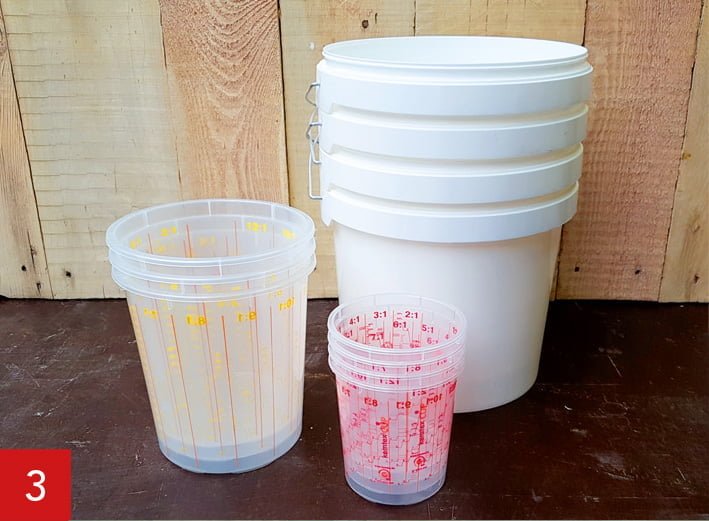
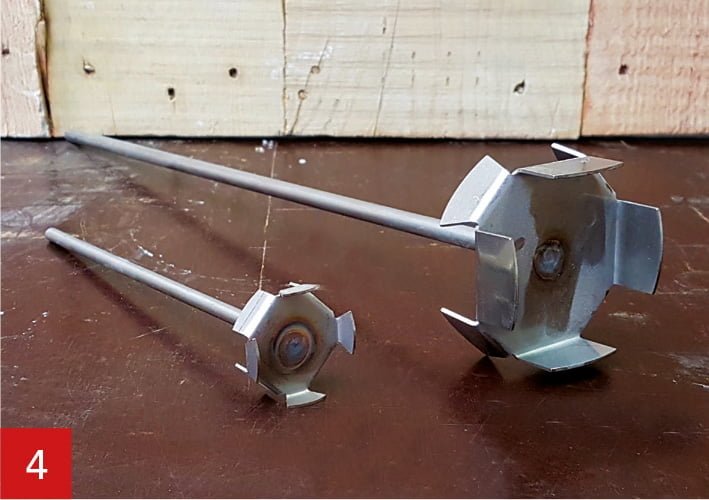
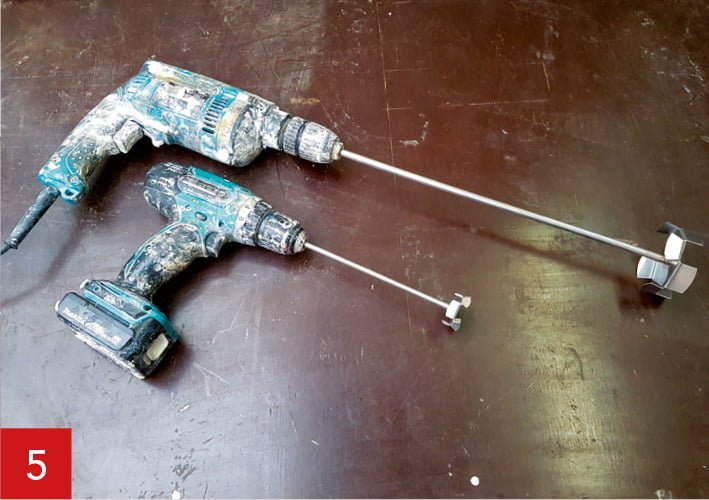
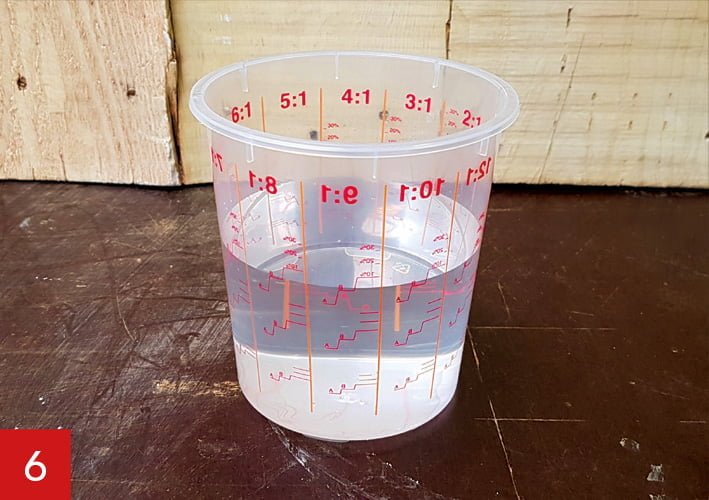
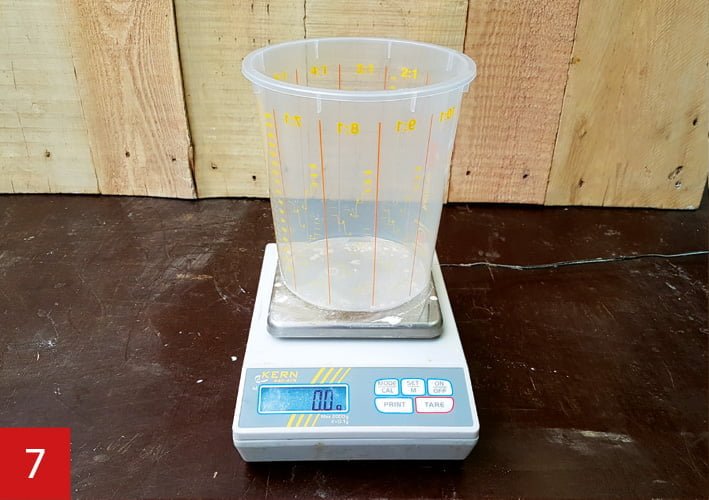
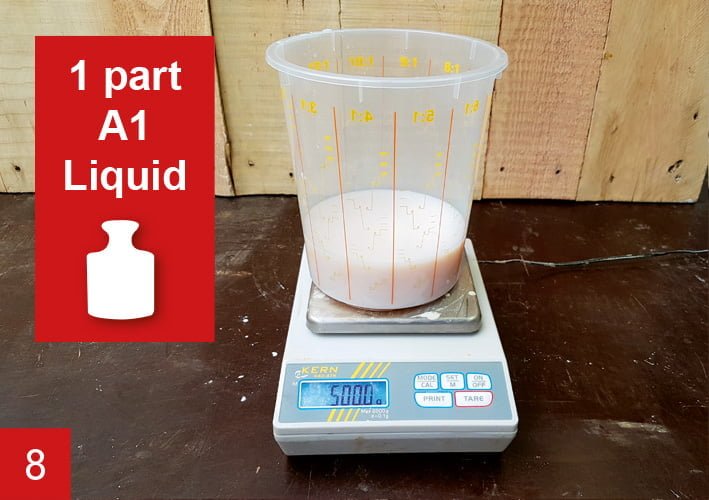
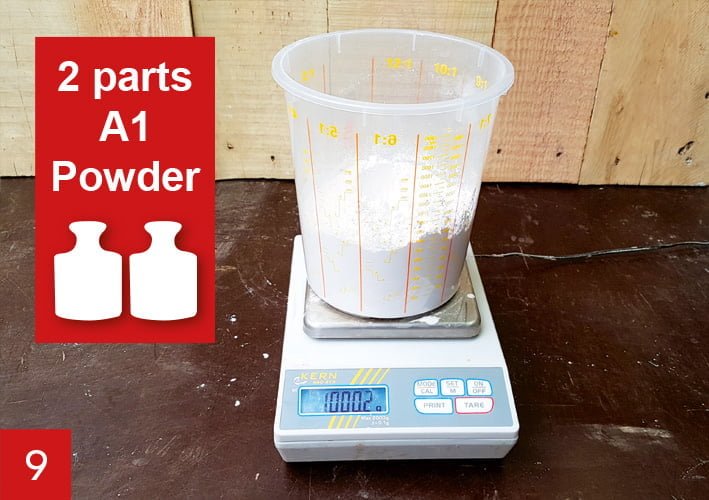
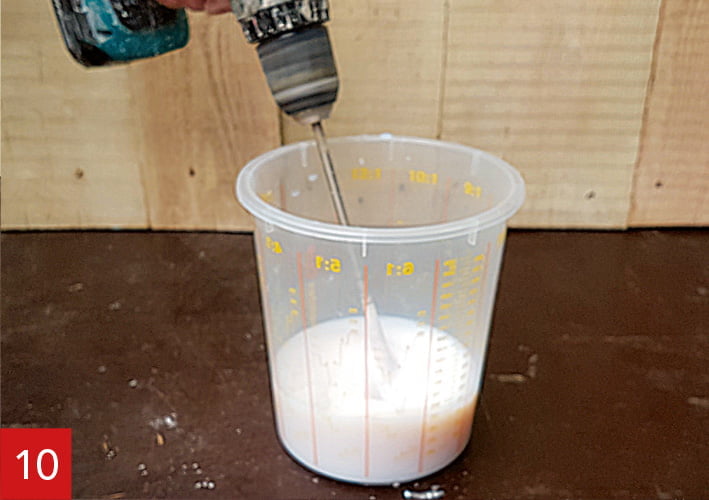
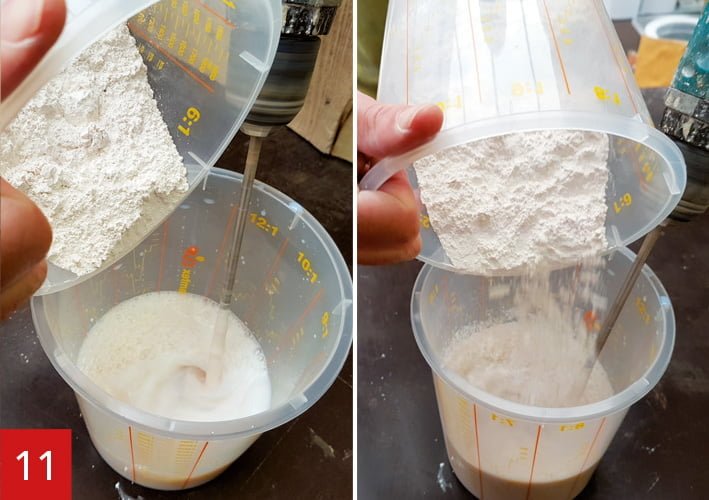
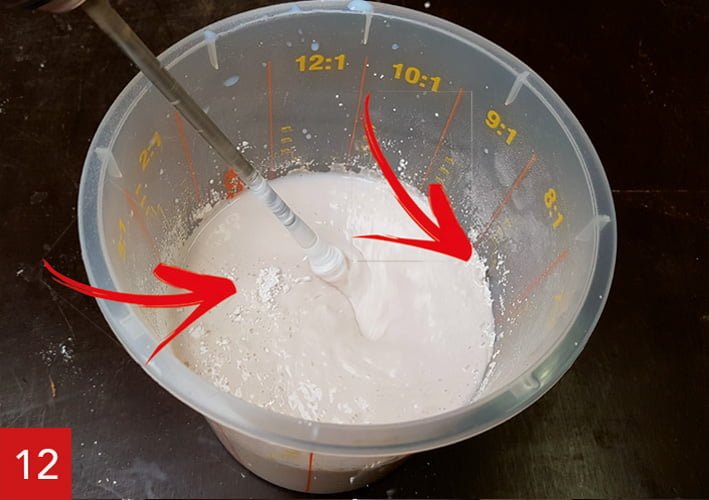
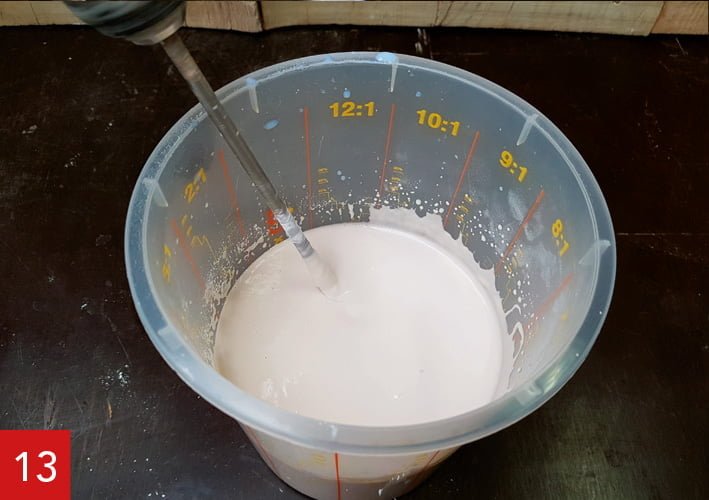
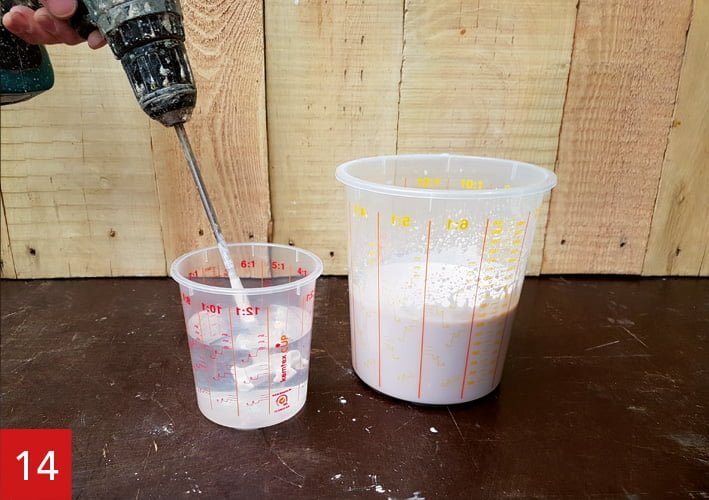
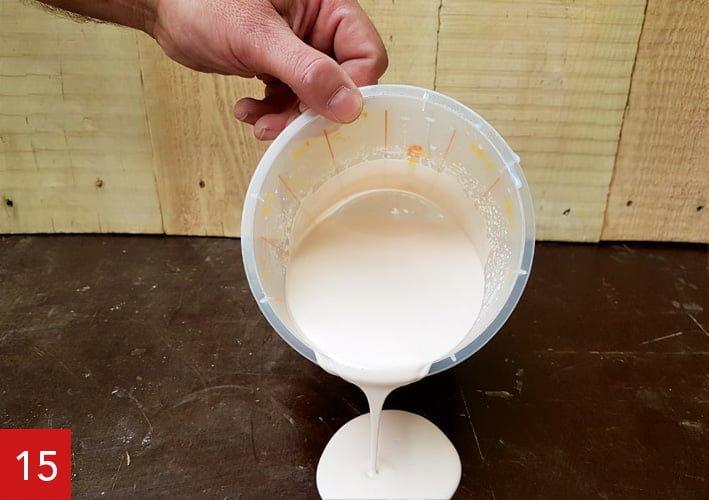